National Safety Month At Ariel Corporation
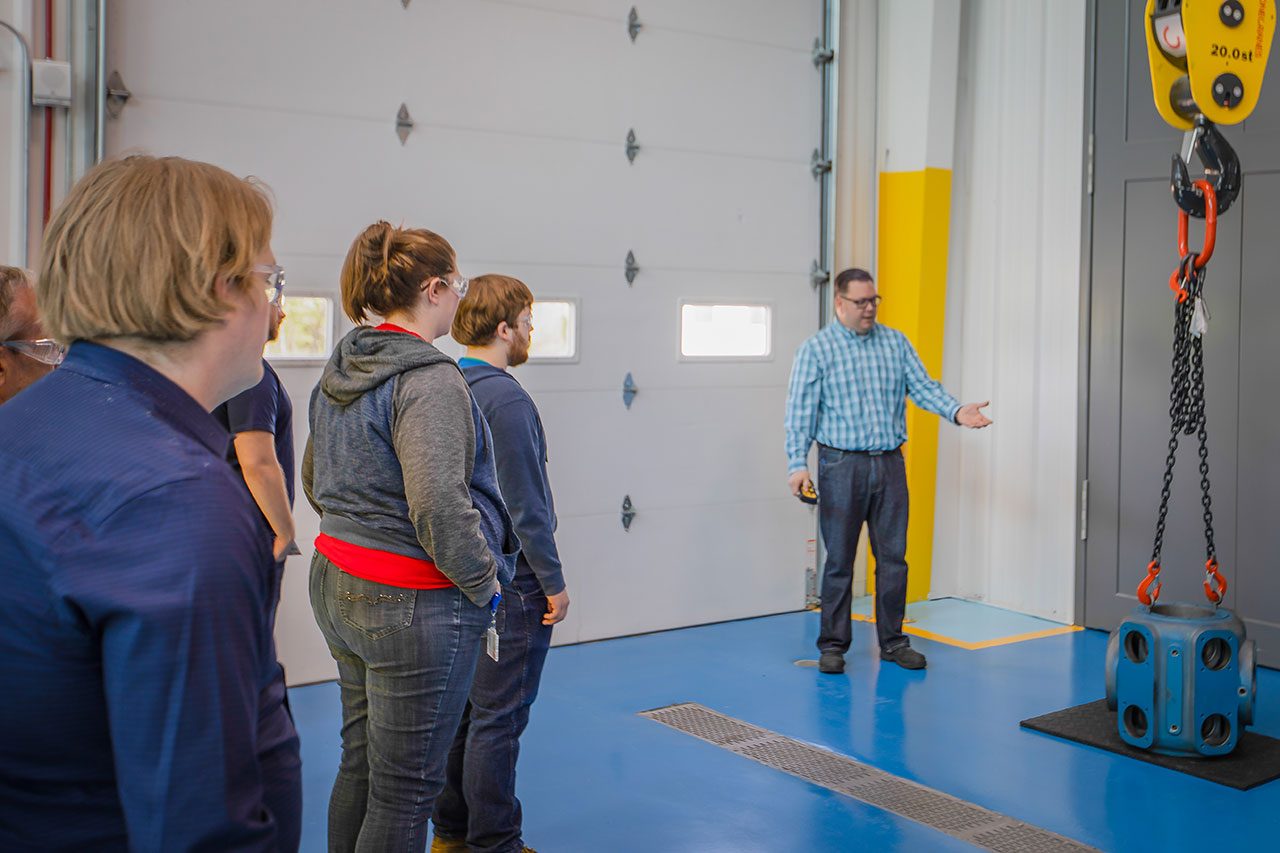
The National Safety Council has declared June National Safety Month. At Ariel, the dedication to employee safety begins before a manufacturing employee starts their job. Employees receive a welcome package in the mail. It includes safety glasses, earplugs, and gloves. That welcome serves as a special message: At Ariel, employee safety is the most important thing we do.
Safety is an around-the-clock priority at Ariel. That long-standing focus is demonstrated in large initiatives and little things that have developed as part of the corporate culture. Employees across the company become eligible for a steel-toed boot voucher once a year. That foot protection is mandatory in every Ariel manufacturing facility. The voucher program grew from the early days of the company when employees got boots from a truck that visited once a year.
Ariel’s Field Services team members wear company-provided steel-toed boots, safety glasses, hearing protection, hard hats, and fire retardant clothing when working at a site and meet any other site requirements end users have. Also, each Ariel Field Services team member is trained in how to handle exposure to highly toxic gases and has thorough training with gas monitoring equipment. The Field Services team also attends SafeLand training, which is recognized by many of Ariel customers and meets many site requirements.
Personal protective equipment (PPE) is prevalent throughout Ariel. In our manufacturing facilities, employees can access PPE from vending machines located in multiple locations throughout the floor. They hold gloves and protection for eyes and ears. The vending machines include company-provided supplies for employee safety and minor health situations.
New manufacturing employees complete their orientation with hours of safety instruction on crane use and forklift operation. The training covers Ariel’s procedures for crane and forklift usage to ensure everyone is operating on the same standards.
First aid supplies are readily available throughout Ariel facilities. Color-coded signage with first aid supplies, including automated external defibrillators (AED) in case of a heart condition on the floor, is painted green and visible throughout Ariel’s manufacturing floor. They are also marked on emergency maps. There is at least one collection of first aid and AED supplies in every Ariel building. Ariel’s larger buildings have first aid kits, with the most located at the World Headquarters at 35 Blackjack Road.
The dedication to safety goes beyond policies and plans. Manufacturing groups discuss injury prevention in pre-shift meetings, and managers often explain any safety issues that happened on opposing shifts. The discussions touched on what caused the accident and how similar incidents can be prevented.
Ariel’s culture has led to an easier implementation of safety standards. Employees take pride in their work and wear the Ariel logo with pride. That makes it easier when Ariel’s Environment, Health and Safety Department of Roger Perry, Jeff Hatch and Quentin Platt discuss a safety initiative. “Ariel has a mentality to go above and beyond minimum requirements in just about everything that we do,” Perry said. “If there is a piece of equipment that needs to be purchased that makes something safer or more efficient, Ariel doesn’t spare the cost on that.”
Action items:
https://www.nsc.org/work-safety/get-involved/national-safety-month