COMPRESSORTECH2 Features Ariel Training
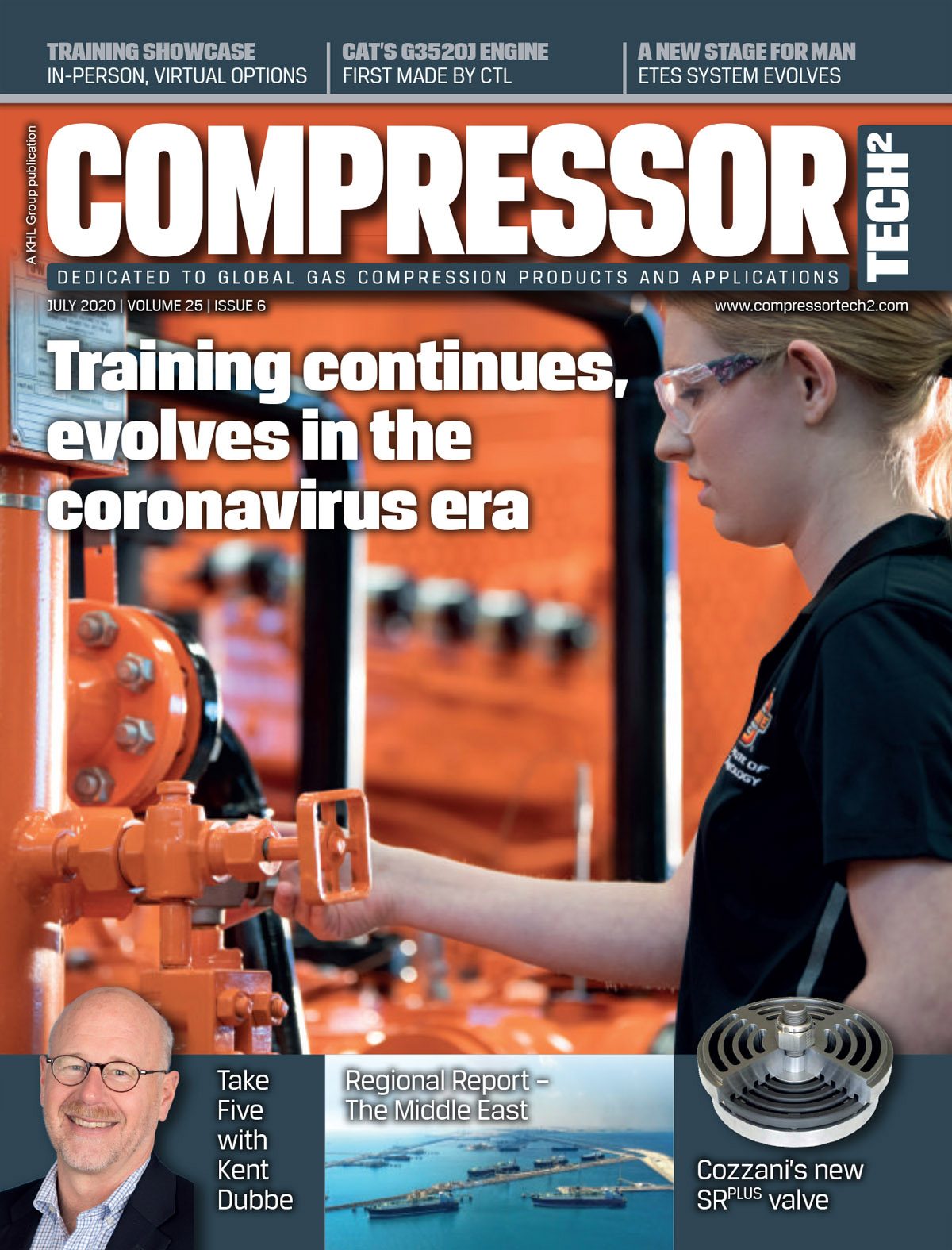
Recruitment, Training Essential to Bring, Retain Great Employees.
By DJ Slater
The following Take Five Q&A was taken from the July 2020 issue of CompressorTech 2 and published with their permission.
Training has always been important to Ariel Corp. In the late 1990s, the company established a dedicated training area on its campus in Mount Vernon, Ohio. But as the years passed and the industry evolved, Ariel realized its training offerings had to follow suit.
In July 2017, Ariel opened the doors to its new training center, featuring 12 classrooms and meeting rooms, three training labs, a theater, and an interactive atrium (see COMPRESSORTECH2, July 2018, p. 32). Kent Dubbe joined Ariel well before this upgrade. As the company’s vice president of Human Resources and Organization Development, Dubbe has seen the company’s training practices evolve from basic courses to deeply involved learning options.
Ariel’s training center has been around for three years. How has it been received within the company and the industry?
The training center was the catalyst for Ariel being able to change the basis of how we develop and conduct training, now having the ability to focus on skill development through hands-on performance demonstration. The machine shop, assembly, and customer technical labs have given customers of the training center – both employees and industrial partners – the chance to practice tasks that they do routinely in their jobs under the guidance of Ariel’s technical instructors and other students.
The result is learning is greatly enhanced through being able to hear about a topic in the classroom, go out, and see that topic demonstrated on industry equipment by the instructor and then practice tasks around that topic as many times as you desire within your training team. So far, the feedback on the training center, and the new training offerings, has been enthusiastically well received.
Training avenues used to be limited solely to in-person events, but now technology allows us to train in ways beyond the classroom. What training does Ariel have, and how does it aid the trainee?
Ariel has faced a challenge in North America and beyond getting the right training, at the right time, to the technicians in the field that aren’t able to travel back to the training center.
For that reason, we have developed alternative offerings of courses and labs through online and mobile venues. In the online world, we have put our front-end program – our basic class – into a highly interactive curriculum that uses modeling and simulation to bring the content alive. The online course has knowledge checks and an online final assessment to assure learning takes place. If a student passes these, they get full credit for the program and don’t need to do the in-person version offered at the training center. In addition, we are expanding this offering by translating the content into Spanish, Chinese, and Russian. Based on the success of the basic program, we are currently exploring other course offerings for development beginning later this year.
As for our mobile training, we are now in our fourth year of running hands-on compression schools in our Mobile Training Lab (MTL). Run almost exclusively in various Texas locations, the MTL allows us to bring our technical instructors from the training center to field locations where groups of mechanics gather to train on Level One mechanic skills in a combined classroom and hands-on style. This industry resource has allowed Ariel to get training to students who have been too busy to travel to Mount Vernon and has allowed them to work on a compressor directly, just as they would do at the training center.
Is one method of training superior to another, or does each method have its place and benefit?
We like to categorize learning into three primary buckets: classroom instruction; hands-on labs, and online experiences. With that in mind, we feel that each of our categories positions a student to succeed. Using our online basic class as a reference, when taking a new student through a variety of technical product and industry information quickly, we have learned that this form of instruction gets the best results and feedback because each student can go at their own pace and concentrate on the areas they need the most. An additional benefit that it offers is saving the customer time, money, and travel, allowing their employees to not have to remove themselves from a week of work in the field or office. Finally, it still accomplishes our primary goal of ensuring that we provide training to everyone who works with Ariel compressors.
Given the above, Ariel still heavily encourages students to visit Ariel’s training center in Mount Vernon, Ohio, to experience the critical product-specific, hands-on learning through our live classroom and lab learning modules. This experience really can’t be replicated in any other format where a technician or engineer can see first-hand what they will deal with in the field and then reinforce it with the practical hands-on practice of applying that learning to an actual compressor just like the ones they will service.
Training has always been important, but isn’t it fair to say that it’s more crucial now than ever before, considering the pandemic will likely cause another talent gap that needs to be filled?
Ariel’s philosophy, whether in good times or bad, is to continually invest in retaining our workforce through the ongoing development of their skill, knowledge, and abilities. To that end, even throughout the unknowns that we are still facing due to the COVID-19 pandemic, our training efforts did not stop. We just adapted our previous learning approaches to meet the new safety and health guidelines. We have been conducting classes and labs, donning face masks, and socially distancing continuously throughout the pandemic.
In addition to our incumbent employees, Ariel still actively engages in training and developing employees in new technical career paths in what we refer to as our “Blue Chip Training Program” – a six month-plus, full-time training commitment designed to upskill new employees in the areas of machining, assembly, and multi-craft maintenance. This pipeline program ensures that we have an ongoing stream of talent going into each of these hard-to-hire career areas made up of employees who not only now possess the necessary technical skills but also understand and value the unique culture of Ariel. We believe strongly that you always need to invest in employees and their development at all times, even COVID-19 times.
Why is it difficult to recruit new blood to the industry?
In talking to other companies, whether in the energy sector or elsewhere, technical jobs across the board have been increasingly more difficult to recruit for as the student base gets smaller and fewer people are drawn to manufacturing or oil and gas. We spend a lot of time on this issue and have had to think way out of the traditional box to provide innovative solutions to how we will address continually growing our talent pipeline for the years ahead.
To start, we have reached out to our local high schools and career centers to partner with them in offering an Ariel-specific high school fundamentals program open to eligible second-semester seniors who are interested in a potential career in manufacturing. We follow that up with offering internships for recent high school graduates; operating a long-term, robust co-op program with multiple colleges for students in engineering, supply chain, manufacturing, and other disciplines; running ongoing Ariel Blue Chip Programs in the areas of machining, assembly and maintenance; and by providing job-specific and degree-granting accredited training to our incumbent employees.
Through these efforts, we can do a solid job in “home-growing” our own future workforce so that we don’t have to only rely as heavily on the recruiting market as our primary source of technical talent.