Carbon Dioxide (CO
2
) may combine with water to form carbonic acid. Carbonic acid is mildly corrosive and at higher pressures can condense into a liquid which will act as a solvent and dilute the cylinder lubrication. The gas properties of the CO
2
mixture should be reviewed at the required operating conditions. Gas properties of CO
2
can be found under the
Gas Properties topic.
See the chart below for recommended materials of construction for piston rods and valves based on suction pressure and CO
2
concentration.
Suction Pressure vs. CO
2
Concentration
Standard or Stainless Piston Rod and Valves Chart
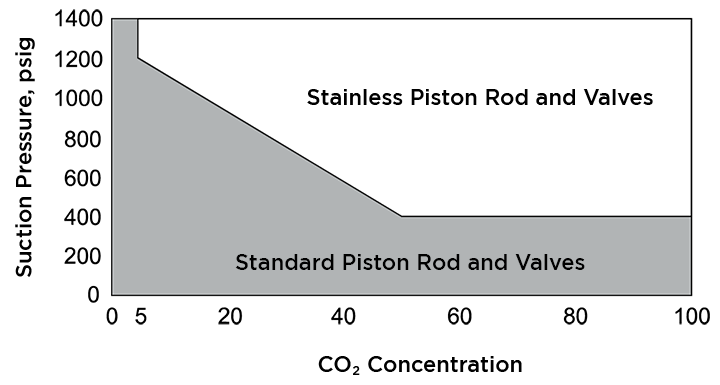
When the standard valve body materials are 416 stainless steel, these are suitable and meet the recommendations of the above chart for CO
2
service. Some valves have carbon steel body material, and would not meet the recommendations for the above chart. The valve material can be found on the cylinder data sheets.
The recommendations for compressor piston rod and valve materials are:
For sweet natural gas with a carbon dioxide concentration less than 5%, or at 5% with a suction pressure less than 1200 psig, or with a carbon dioxide concentration up to 50% with a suction pressure less than 400 psig, or with any suction pressure lower than 400 psig, use standard piston rod and valve materials.
For sweet natural gas with a carbon dioxide concentration outside the above limits, use 17-4PH stainless steel piston rods and stainless steel compressor valves. Most valve bodies are 416 stainless steel material and will meet the recommendations for stainless steel in CO
2
service. When the standard valve body material is carbon steel, the 17-4PH stainless steel valve option should be chosen. (When changing to the 17-4PH valve material option, it is recommended that standard valves be used for unit start-up. Once the system is confirmed clean, the stainless steel valves should be installed).
CO
2
is soluble in mineral oils, thereby reducing the oil / gas mixture viscosity. Mineral oils are completely miscible into CO
2
, which reduces the effectiveness of the oil. Compounding mineral oils or PAG (poly-alkaline-glycol) synthetic lubricants are commonly used. See Cylinder and Packing Lubrication Requirements in the Ariel
Packager Standards and contact Ariel in Mount Vernon for a recommendation.
Compression of carbon dioxide often involves operating conditions that are near or above the critical point of the gas. The gas properties will be very sensitive to small changes in pressures and temperatures when near and above the critical point. When a stage suction pressure is near the critical pressure, allow a greater margin from the critical temperature for more stable gas properties. This may mean operating at a suction temperature of 40 to 50 F (20 to 30 C) above the critical temperature. When a stage suction pressure is above the critical pressure, allow enough suction temperature to maintain proper gas properties. Proper gas properties means maintaining a suction compressibility (Z) value above 0.4, and preferably above 0.5. In this "dense phase" region above the critical pressure the gas can have properties of either a gas or a liquid and the density of the gas will fluctuate greatly with small changes in pressure or temperature.
Due to the sensitivity of the gas properties to small changes in pressure and temperature in this "dense phase" region, near and above the critical point, the interstage temperature may need to be controlled. If the gas suction temperature is allowed to vary, the gas density will fluctuate widely and can cause large changes in the acoustical response of the gas piping system. This can lead to acoustic force driven shaking of the equipment.
Critical pressure and temperature are provided on the phase envelope within the Ariel Performance Program.
A controlled temperature system can be accommodated during higher ambient temperature swings through gas cooler louvers and fan control. If this is not enough to control the gas temperature out of the cooler, hot air recirculation or heaters may need to be provided in the cooler design. Controlling with a bypass around the gas cooler with a temperature control valve allowing mixing of hot and cold gas may not be suitable, if the cooled gas condenses in the cooler.
When selecting a compressor for carbon dioxide service, lower piston speeds may be necessary in order to allow the heavier gas to flow through the valves with proper valve dynamics. The lower piston speeds will lower the pseudo-q values as well as improve the efficiency of the unit (lowering the power per unit flow value).